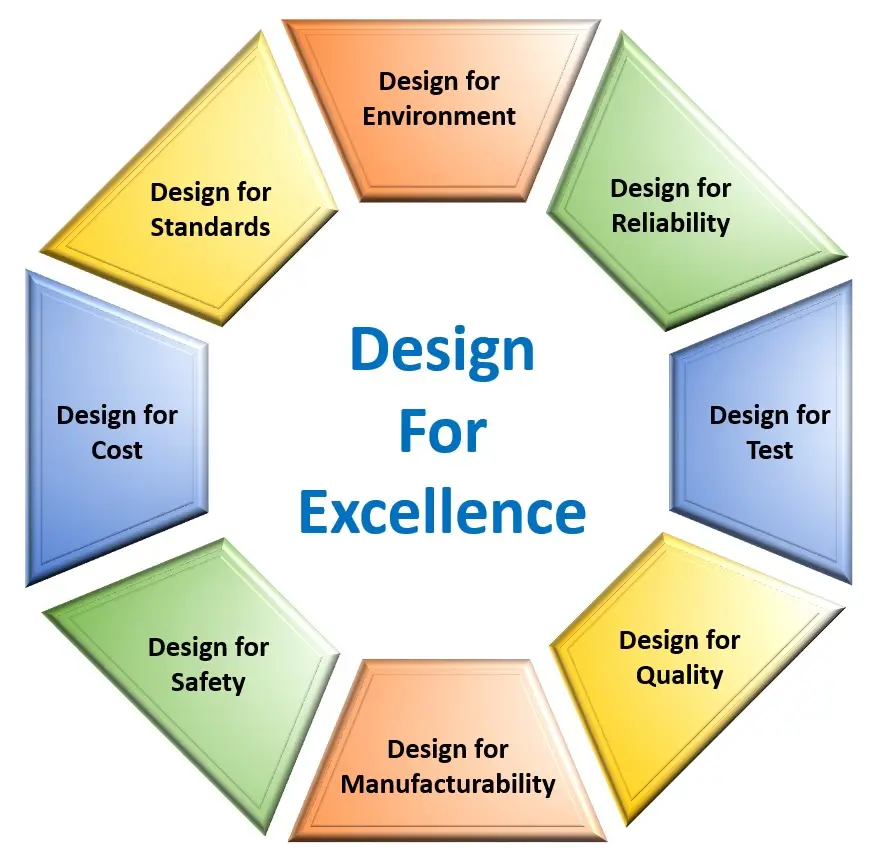
“Principles of Effective Mechanical Design: A Beginner's Guide-2024”
Introduction
In essence, the significance of mechanical design lies in comprehending the essential aspects that determine the success of a component. It involves gaining insights into the size, visual aesthetics, shape, and standardized dimensions of the component. Additionally, understanding the materials used, machining requirements, tolerances, assembly processes, and relevant considerations for welding are crucial components of effective mechanical design. By delving into these elements, beginners can grasp the foundations of mechanical design, enabling them to create components that meet industry standards and exhibit optimal performance.
What are the role of good Mechanical design in creating reliable and efficient mechanical systems.
Enhanced Reliability in Good Design
- Robust Component Selection:
- Well-designed systems choose components with optimal strength and durability, reducing the risk of failures and ensuring long-term reliability.
- Minimized Stress Points:
- Careful design minimizes stress concentrations, preventing premature fatigue and component failure, ultimately enhancing the reliability of the system.
- Redundancy:
- Good design incorporates redundancy where possible, providing backup components or systems to take over in case of a primary component failure, thus improving overall system reliability.
- Ease of Maintenance:
- Well-designed systems consider maintenance from the start, incorporating features for easy access to components. This ensures quick inspections, repairs, or replacements, minimizing downtime and promoting smooth operation."
Improved Efficiency in Good Design
- Optimized Component Integration:
- Well-designed systems ensure seamless collaboration among components, minimizing energy losses from friction or inefficient power transfer. This enhances overall system efficiency.
- Advanced Material Selection:
- Good design considers the use of lightweight and high-performance materials, reducing system weight, lowering energy consumption, and elevating overall efficiency.
- Aerodynamics and Fluid Dynamics:
- In systems involving air or fluid flow, good design incorporates aerodynamic or fluid dynamic principles. This minimizes resistance and optimizes flow characteristics, contributing to a more efficient system.
- Friction Reduction:
- Design elements like bearings, lubricants, and smooth surfaces are integrated to minimize friction. This results in reduced energy losses and an improved overall system efficiency.
Additional Benefits of Good Design:
- Cost-Effectiveness:
- Well-designed systems are cost-effective due to reduced maintenance needs and fewer breakdowns, resulting in lower long-term operating costs.
- Safety:
- Good design prioritizes safety by identifying and addressing potential hazards. The incorporation of safety features ensures a secure system for operators and those in the vicinity.
- Sustainability:
- Efficient systems designed with sustainability in mind consume less energy, minimizing their environmental impact. Additionally, well-designed systems may facilitate easier disassembly and recycling at the end of their lifespan.
1. Understanding the Basics of Mechanical Design
The design and its significance in various industries.
The Design: The Backbone of Machines
Mechanical design is the process of translating ideas and functionalities into functional, physical machines or systems. It involves a blend of creativity, engineering principles, and practical considerations to bring a product from concept to reality. Here's a breakdown of its significance across various industries
Core of Product Development:
- Foundation for Manufacturing:
- Mechanical design lays the groundwork for efficient and cost-effective manufacturing. Detailed drawings, specifications, and material selection ensure the product can be produced reliably and consistently.
- Functionality and Performance:
- It dictates how well a product performs its intended function. Through careful design, engineers ensure the system operates smoothly, delivers desired outputs, and meets performance expectations.
- Manufacturing:
- From complex production lines in automotive plants to automated machinery in food processing facilities, mechanical design is essential for creating efficient and high-volume production systems.
- Aerospace:
- Airplanes, rockets, and satellites rely heavily on meticulously designed mechanical systems for propulsion, control, and structural integrity. Even minor design flaws can have catastrophic consequences in this industry.
- Consumer Products:
- From the intricate mechanisms in a toaster to the robust structure of a car, mechanical design shapes the functionality, durability, and user experience of everyday products.
- Robotics:
- The field of robotics heavily utilizes mechanical design to create robots that can move, interact with their environment, and perform complex tasks.
- Goal: Ensure the system effectively serves its intended purpose, considering outputs, motions, and forces.
- Considerations: Load capacity, power requirements, accuracy, efficiency, user experience.
- Goal: Select materials with appropriate strength, weight, and durability to withstand anticipated loads and stresses.
- Considerations: Tensile strength, yield strength, fatigue resistance, corrosion resistance, weight.
- Goal: Understand mechanics principles (statics, dynamics, kinematics) to design mechanisms producing desired motion and forces.
- Considerations: Forces, moments, friction, center of gravity, gear ratios, linkages.
- Goal: Ensure practical, cost-effective manufacturing with components easy to fabricate, assemble, and maintain.
- Considerations: Complexity of shapes, tolerances, assembly procedures, tooling requirements.
- Goal: Prioritize safety, minimizing hazards and incorporating features to prevent injuries during operation and maintenance.
- Considerations: Sharp edges, pinch points, moving parts exposure, pressure vessels, emergency shut-off mechanisms.
- Goal: Balance design parameters (weight, cost, performance, efficiency) to optimize the system.
- Considerations: Lightweight materials, efficient power transfer, minimizing friction losses.
- Goal: Recognize the non-linear design process, involving prototypes, real-world testing, and refining based on results.
- Considerations: Computer simulations, prototyping techniques, testing procedures, data analysis.
- Goal: Consider environmental impact throughout the product lifecycle, utilizing eco-friendly materials and designing for easy disassembly and recycling.
- Considerations: Eco-friendly materials, waste reduction in production, easy disassembly, recycling design.
- Provides Direction and Focus: Clear goals act as a compass, guiding the entire design process. Everyone involved understands what the project is trying to achieve, ensuring everyone's efforts are aligned and focused on the desired outcome.
- Improves Communication and Collaboration: When goals and requirements are well-defined, it fosters better communication and collaboration among designers, developers, stakeholders, and clients. Everyone has a shared understanding of the project's objectives, leading to more efficient decision-making and fewer misunderstandings.
- Reduces Risk of Scope Creep: Scope creep is when the project's scope expands beyond its original intent, often leading to delays and budget overruns. Clearly defined goals and requirements help keep everyone on the same page and prevent the project from veering off course.
- Measures Success: How do you know if your design is successful? Defined goals provide a yardstick to measure success. You can assess how well the final product meets the initial objectives and user needs.
- Prioritizes Features: With clear goals, you can prioritize features based on their relevance to achieving those goals. This helps allocate resources effectively and ensures the most important features are developed first.
- Reduces Rework: Ambiguous goals or requirements often lead to designs that miss the mark. Having clear goals upfront minimizes the need for rework and revisions later in the process, saving time and resources.
- Sets Expectations: Clearly defined goals help manage client or stakeholder expectations. Everyone involved has a realistic understanding of what the project will and won't deliver.
- 1. Identifying Needs and User Personas
- 2. Prioritizing Features and Functionality
- 3. Material Selection and Durability
- 5. Safety Considerations
- 6. Design for Maintainability and Serviceability
- 7. Environmental Impact
- 8. Testing and Refinement
- Function: What is the primary function of the component or system? (e.g., load-bearing, motion transmission, heat transfer)
- Operating Conditions: Consider factors like temperature, pressure, vibrations, chemicals, and moisture.
- Loading Conditions: Identify the forces or stresses the material will experience (static, dynamic, or both).
- Design Constraints: Are there size, weight, or shape limitations influencing material selection?
- Performance Requirements: Specify wear resistance, corrosion resistance, or other essential properties.
- Cost: Consider the budget for the project; material cost is a significant factor.
- Sustainability: Consider environmental factors like recyclability, biodegradability, and the material's source.
- Based on requirements, research potential materials using databases, handbooks, and online resources.
- Common material categories: Metals, Polymers, Ceramics, Composites.
- Compare shortlisted materials based on relevant properties (mechanical, physical, chemical, processing).
- Consider using material selection charts or software tools to compare and prioritize materials.
- Example: Ashby Charts.
- Assess the feasibility of manufacturing the final product with the chosen material.
- Consider machining, fabrication, and cost.
- Perform physical testing on material samples to validate suitability (tensile tests, fatigue tests, corrosion tests).
- Create prototypes using the chosen material to test real-world performance.
- Select the most suitable material based on evaluation and testing results.
- Document the material selection process and rationale for future reference and communication.
- Availability: Consider the availability and lead time for obtaining the chosen material.
- Regulations: Check for industry-specific regulations regarding materials used in certain products.
- Sustainability: Choose materials with lower environmental impact whenever possible.
- Material Selection: Good design begins with choosing materials that offer high strength-to-weight ratios. For example:
- Steel Alloys: Used in bridges, machinery, and structural components due to their exceptional strength.
- Titanium: Known for its strength, corrosion resistance, and lightweight properties.
- Composite Materials: Combine different materials to achieve strength while minimizing weight.
- Structural Integrity: Well-designed components distribute loads efficiently, preventing stress concentrations and ensuring long-term strength.
- Safety Factors: Designers incorporate safety margins to handle unexpected loads or variations.
- Corrosion Resistance: Proper material selection (e.g., stainless steel, coatings) prevents degradation due to environmental factors.
- Fatigue Resistance: Designing for cyclic loading (e.g., in aircraft wings) ensures durability over millions of cycles.
- Wear Resistance: Good design minimizes wear through proper lubrication, surface treatments, and material choices.
- Maintenance Considerations: Easy access for maintenance and replacement prolongs system life.
- Lifecycle Cost Analysis: Good design balances initial costs with long-term savings. For instance:
- Investment in Quality: Spending more upfront on reliable components reduces maintenance and replacement costs.
- Energy Efficiency: Efficient designs save operational costs over time.
- Predictive Maintenance: Identifying issues early prevents costly breakdowns.
- Sustainable Design: Considering the entire lifecycle (from production to disposal) ensures cost-effectiveness.
- Standardization: Using common components reduces manufacturing costs.
- Design for Manufacturing (DFM): Streamlining production processes minimizes expenses.
- Understanding User Needs
- Empathy
- Iterative Design
- Focus on Usability
- Accessibility
- Simpler Designs: Products with fewer parts, simpler shapes, and efficient assembly processes require less material, labor, and machine time to manufacture. This translates to significant cost savings in production.
- Minimized Waste: Easy-to-manufacture designs often generate less scrap material during production. This not only reduces costs but also promotes sustainability.
- Faster Production Times: Products that are straightforward to produce can be manufactured more quickly, allowing businesses to meet higher demand and potentially capture market opportunities faster.
- Reduced Complexity: Fewer components and simpler designs lead to a lower risk of errors during assembly. This contributes to improved product quality and overall reliability.
- Increased Consistency: Easier manufacturing processes are more repeatable, leading to consistent product quality across different production batches.
- Flexibility for High Volume: Designs that are easy to manufacture can be readily scaled up for high-volume production to meet increased demand. This allows businesses to capitalize on market success efficiently.
- Simplified Supply Chain: Fewer components often translate to a less complex supply chain. This can make it easier to manage inventory levels and reduce potential disruptions.
- Competitive Pricing: Cost savings from efficient manufacturing can be passed down to consumers in the form of more competitive pricing.
- Better Availability: Easier-to-manufacture products are more likely to be readily available for purchase due to faster production times and increased scalability.
- Improved Product Value: Consumers get products that are not only functional but also well-made and affordable, offering a better overall value proposition.
- Standardization of Components: Using readily available, standardized components simplifies sourcing and reduces the need for custom parts.
- Modular Design: Breaking down a product into easily assembled modules allows for flexibility in customization and future upgrades.
- 3D Printing: For some products, 3D printing allows for complex designs with fewer parts, potentially simplifying production.
- Prototypes expose issues early in the design process, allowing for corrections and improvements before significant resources are invested.
- Prototypes allow you to physically test if the design works as intended, revealing potential flaws in motion, load handling, or user interaction.
- Prototypes can be used to gather valuable user feedback on usability, ergonomics, and overall user experience.
- Simulates real-world use to assess if the design performs its intended function effectively.
- Pushes the prototype beyond normal operating conditions to identify weaknesses and ensure durability.
- Observes users interacting with the prototype to evaluate ease of use and identify areas for improvement.
- Too Loose: Excessive tolerance can lead to parts that don't fit together properly, causing excessive wear, vibration, or performance issues. Imagine a loose bearing allowing too much movement in a rotating shaft.
- Too Tight: Extremely tight tolerances can be difficult and expensive to manufacture, potentially increasing production costs and lead time. It might also result in parts that bind or seize due to slight variations.
- Tighter tolerances require more precise manufacturing processes, which can be expensive and time-consuming.
- Looser tolerances allow for more variation during production, potentially simplifying manufacturing but impacting functionality if not managed carefully.
- Function First: Prioritize functionality. Identify critical dimensions where tight tolerances are essential for proper operation.
- Consider Manufacturing Capabilities: Understand the capabilities of your chosen manufacturing process. Don't specify tolerances that are too tight for the process to achieve consistently.
- Standardization: Whenever possible, use standard tolerance grades as defined by industry standards. This simplifies communication with manufacturers and reduces costs.
- Cost-Benefit Analysis: Evaluate the trade-off between tighter tolerances and the resulting increase in cost and complexity. Aim for the loosest tolerance possible while maintaining functionality.
- Tolerance Stack-Up: Consider the cumulative effect of tolerances throughout the assembly. Small variations in multiple components can add up, potentially causing issues. Analyze tolerance stack-up to ensure final assembly dimensions fall within acceptable limits.
- Detailed documentation minimizes ambiguity and ensures everyone is on the same page. Drawings, specifications, and assembly instructions leave little room for misinterpretation, preventing costly errors and delays.
- Clear documentation acts as a shared reference point, enabling team members across disciplines to collaborate effectively. Designers can communicate their ideas clearly, while engineers and manufacturers understand the requirements for production.
- Well-documented designs are easier to understand for future engineers or designers who may need to modify or maintain the product. This knowledge transfer ensures the product's longevity and reduces the risk of errors during future iterations.
- Precise technical drawings and specifications guide the manufacturing process. Manufacturers can efficiently translate design intent into reality, minimizing production errors and ensuring consistent quality.
- These powerful tools allow designers to create detailed two-dimensional (2D) drawings and three-dimensional (3D) models. Popular CAD software includes AutoCAD, SolidWorks, and Inventor.
- Standardized formats like ANSI or ISO ensure drawings are consistent and universally understood. These standards define conventions for dimensioning, symbols, and annotations.
- A BOM is a list of all the parts and components required to assemble a product. It includes details like part numbers, quantities, and specifications.
- Clear instructions with illustrations guide the assembly process step-by-step. This ensures the product is assembled correctly and functions as intended.
- Platforms like Trello or Asana can be used to manage documentation, track revisions, and facilitate communication within the design team.
- "Engineering Mechanics: Dynamics" by J.L. Meriam and L.G. Kraige - This comprehensive textbook provides a thorough exploration of dynamics principles essential for mechanical design.
- "Shigley's Mechanical Engineering Design" by Richard G. Budynas and Keith J. Nisbett - Widely regarded as a standard in the field, this book offers practical insights into mechanical engineering design concepts and applications.
Significance Across Industries:
The fundamental principles that govern design.
1. Functionality and Performance:
2. Strength of Materials:
3. Mechanics of Motion:
4. Design for Manufacturability (DFM):
5. Design for Safety:
6. Optimization:
7. Iteration and Testing:
8. Sustainability:
2. Design Intent and Requirements:
Clearly defining design goals and requirements is absolutely essential for the success of any design project. It's like building a house – you wouldn't start construction without a blueprint, would you? Here's why having well-defined goals and requirements is so important:
Here's an analogy: Imagine designing a website. Without clear goals (e.g., increase sales, improve user engagement), you might end up with a beautiful website that no one uses. But with defined goals, you can design a website that is not only aesthetically pleasing but also drives conversions and keeps users coming back.
In conclusion, taking the time to clearly define design goals and requirements upfront is an investment that pays off throughout the entire design process. It leads to a more focused, efficient, and successful project with a higher chance of achieving its desired outcomes.
Understanding the intended use and functionality informs the design process.
3. Material Selection
1. Define Requirements:
2. Research Candidate Materials:
3. Evaluate and Compare Materials:
4. Use Selection Tools (Optional):
5. Consider Manufacturing Considerations:
6. Testing and Prototyping:
7. Final Selection and Documentation:
Additional Considerations:
1. Strength:
2. Durability:
3. Cost-Effectiveness:
1. Define Requirements:
2. Research Candidate Materials:
3. Evaluate and Compare Materials:
4. Use Selection Tools (Optional):
5. Consider Manufacturing Considerations:
6. Testing and Prototyping:
7. Final Selection and Documentation:
Additional Considerations:
1. Strength:
2. Durability:
3. Cost-Effectiveness:
In summary, good design directly impacts the strength, durability, and cost-effectiveness of mechanical systems. It's a delicate balance that requires expertise, creativity, and a holistic approach. 🛠️💡
4. Ergonomics and User-Centered Design
The concept of designing with the end user in mind.
Designing with the end user in mind, also known as user-centered design (UCD) or human-centered design (HCD), is a philosophy that places the needs, wants, and limitations of the end user at the forefront of the design process. It's about creating products, services, or experiences that are not only functional but also intuitive, user-friendly, and enjoyable to interact with.
Here are some key principles of designing with the end user in mind:
How ergonomic principles contribute to better user experiences.
Ergonomics plays a critical role in crafting user experiences that are not only functional but also comfortable, efficient, and satisfying. Here's how ergonomic principles contribute to better user experiences:
5. Design for Manufacturability
Significance of Designing Products for Easy Manufacturing & cost-effective manufacturing processes and techniques.
Reduced Production Costs:
Enhanced Quality and Reliability:
Improved Scalability:
Benefits for Consumers:
Examples of Design for Manufacturability (DFM):
6. Prototyping and Testing:
Prototyping: Validating Mechanical Design Ideas
Early Problem Detection:
Functionality Testing:
User Feedback:
Testing Methods in Mechanical Design:
Functional Testing:
Stress Testing:
Usability Testing:
By combining prototyping and testing, mechanical engineers refine designs iteratively, ensuring they are functional, reliable, and user-friendly before final production.
7. Consideration of Tolerances:
Tolerances: Balancing Functionality and Manufacturability
Impact on Functionality:
Impact on Manufacturability:
Tips for Setting Appropriate Tolerances:
By carefully considering these factors, you can set appropriate tolerances that ensure your design functions flawlessly while remaining cost-effective and manufacturable. Remember, the goal is to find the sweet spot between precision and practicality.
8. Documentation and Communication:
Clear Documentation: The Bridge to Successful Products
Eliminates Misunderstandings:
Facilitates Collaboration:
Knowledge Transfer:
Streamlines Manufacturing:
Tools for Communicating Design Through Documentation
Computer-Aided Design (CAD) Software:
Engineering Drawing Standards:
Bill of Materials (BOM):
Assembly Instructions:
Project Management Tools:
By leveraging these tools and emphasizing clear communication through documentation, design teams can bridge the gap between concept and reality, ensuring a smooth journey from design intent to a successful product.
In wrapping up, delving into the fundamental principles of mechanical design is paramount for crafting dependable, efficient, and innovative systems. By prioritizing functionality, material strength, motion mechanics, manufacturability, safety, optimization, iteration, and sustainability, engineers can fashion solutions that meet the complexities of modern engineering challenges.
To further enrich your understanding, consider exploring the following recommended resources:
For those seeking interactive learning experiences, online platforms such as Coursera, Udemy, or LinkedIn Learning offer a variety of courses covering different facets of mechanical design.
I invite you to share your thoughts, questions, or experiences in the comments section below. Let's continue the dialogue and benefit from each other's perspectives. Thank you for accompanying me on this journey through mechanical design principles.
Ergonomics plays a critical role in crafting user experiences that are not only functional but also comfortable, efficient, and satisfying. Here's how ergonomic principles contribute to better user experiences:
5. Design for Manufacturability
Significance of Designing Products for Easy Manufacturing & cost-effective manufacturing processes and techniques.
Reduced Production Costs:
Enhanced Quality and Reliability:
Improved Scalability:
Benefits for Consumers:
Examples of Design for Manufacturability (DFM):
6. Prototyping and Testing:
Prototyping: Validating Mechanical Design Ideas
Early Problem Detection:
Functionality Testing:
User Feedback:
Testing Methods in Mechanical Design:
Functional Testing:
Stress Testing:
Usability Testing:
By combining prototyping and testing, mechanical engineers refine designs iteratively, ensuring they are functional, reliable, and user-friendly before final production.
7. Consideration of Tolerances:
Tolerances: Balancing Functionality and Manufacturability
Impact on Functionality:
Impact on Manufacturability:
Tips for Setting Appropriate Tolerances:
By carefully considering these factors, you can set appropriate tolerances that ensure your design functions flawlessly while remaining cost-effective and manufacturable. Remember, the goal is to find the sweet spot between precision and practicality.
8. Documentation and Communication:
Clear Documentation: The Bridge to Successful Products
Eliminates Misunderstandings:
Facilitates Collaboration:
Knowledge Transfer:
Streamlines Manufacturing:
Tools for Communicating Design Through Documentation
Computer-Aided Design (CAD) Software:
Engineering Drawing Standards:
Bill of Materials (BOM):
Assembly Instructions:
Project Management Tools:
By leveraging these tools and emphasizing clear communication through documentation, design teams can bridge the gap between concept and reality, ensuring a smooth journey from design intent to a successful product.
In wrapping up, delving into the fundamental principles of mechanical design is paramount for crafting dependable, efficient, and innovative systems. By prioritizing functionality, material strength, motion mechanics, manufacturability, safety, optimization, iteration, and sustainability, engineers can fashion solutions that meet the complexities of modern engineering challenges.
To further enrich your understanding, consider exploring the following recommended resources:
For those seeking interactive learning experiences, online platforms such as Coursera, Udemy, or LinkedIn Learning offer a variety of courses covering different facets of mechanical design.
I invite you to share your thoughts, questions, or experiences in the comments section below. Let's continue the dialogue and benefit from each other's perspectives. Thank you for accompanying me on this journey through mechanical design principles.
Здравствуйте! Меня зовут Шестаков Юрий Иванович, я дерматолог с многолетним опытом работы в области эстетической медицины. Сегодня я отвечу на ваши вопросы и расскажу полезной информацией о лазерном удалении папиллом. Моя цель — помочь вам понять, как безопасно и эффективно избавиться от папиллом и какие преимущества имеет лазерное удаление.
Какие существуют методы профилактики появления папиллом?
Для профилактики появления папиллом рекомендуется поддерживать высокий уровень гигиены, избегать контакта с инфицированными поверхностями, использовать индивидуальные предметы личной гигиены и регулярно посещать врача для осмотра кожи. Важную роль играет укрепление иммунной системы через правильное питание и здоровый образ жизни.
What are the methods for preventing the appearance of papillomas?
To prevent the appearance of papillomas, it is recommended to maintain a high level of hygiene, avoid contact with infected surfaces, use personal hygiene items, and regularly visit a doctor for skin examinations. Strengthening the immune system through proper nutrition and a healthy lifestyle also plays an essential role.